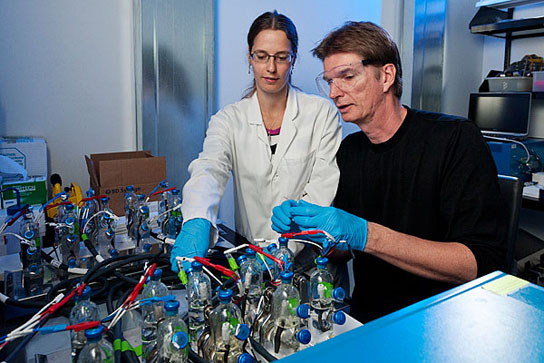
Post-doctoral fellow Svenja Lohner, left, and Professor Alfred Spormann. Their research, along with the work of others, could help solve one of the biggest challenges for large-scale renewable energy: What to do with surplus electricity generated by photovoltaic power stations and wind farms. L.A. Cicero
Taking a “greener” approach to methane production, scientists from Stanford and Pennsylvania State are raising colonies of microorganisms, called methanogens, which have the ability to turn electrical energy into pure methane in microbial process that is carbon neutral.
Microbes that convert electricity into methane gas could become an important source of renewable energy, according to scientists from Stanford and Pennsylvania State universities.
Researchers at both campuses are raising colonies of microorganisms, called methanogens, which have the remarkable ability to turn electrical energy into pure methane – the key ingredient in natural gas. The scientists’ goal is to create large microbial factories that will transform clean electricity from solar, wind or nuclear power into renewable methane fuel and other valuable chemical compounds for industry.
“Most of today’s methane is derived from natural gas, a fossil fuel,” said Alfred Spormann, a professor of chemical engineering and of civil and environmental engineering at Stanford. “And many important organic molecules used in industry are made from petroleum. Our microbial approach would eliminate the need for using these fossil resources.”
Stanford Professor Alfred Spormann explains how the system works.
While methane itself is a formidable greenhouse gas, 20 times more potent than CO2, the microbial methane would be safely captured and stored, thus minimizing leakage into the atmosphere, Spormann said.
“The whole microbial process is carbon neutral,” he explained. “All of the CO2 released during combustion is derived from the atmosphere, and all of the electrical energy comes from renewables or nuclear power, which are also CO2-free.”
Methane-producing microbes, he added, could help solve one of the biggest challenges for large-scale renewable energy: What to do with surplus electricity generated by photovoltaic power stations and wind farms.
“Right now there is no good way to store electricity,” Spormann said. “However, we know that some methanogens can produce methane directly from an electrical current. In other words, they metabolize electrical energy into chemical energy in the form of methane, which can be stored. Understanding how this metabolic process works is the focus of our research. If we can engineer methanogens to produce methane at scale, it will be a game changer.”
‘Green’ methane
Burning natural gas accelerates global warming by releasing carbon dioxide that’s been trapped underground for millennia. The Stanford and Penn State team is taking a “greener” approach to methane production. Instead of drilling rigs and pumps, the scientists envision large bioreactors filled with methanogens – single-cell organisms that resemble bacteria but belong to a genetically distinct group of microbes called archaea.
By human standards, a methanogen’s lifestyle is extreme. It cannot grow in the presence of oxygen. Instead, it regularly dines on atmospheric carbon dioxideand electrons borrowed from hydrogen gas. The byproduct of this microbial meal is pure methane, which methanogens excrete into the atmosphere.
The researchers plan to use this methane to fuel airplanes, ships and vehicles. In the ideal scenario, cultures of methanogens would be fed a constant supply of electrons generated from emissions-free power sources, such as solar cells, wind turbines and nuclear reactors. The microbes would use these clean electrons to metabolize carbon dioxide into methane, which can then be stockpiled and distributed via existing natural gas facilities and pipelines when needed.
When the microbial methane is burnt as fuel, carbon dioxide would be recycled back into the atmosphere where it originated from – unlike conventional natural gas combustion, which contributes to global warming.
“Microbial methane is much more ecofriendly than ethanol and other biofuels,” Spormann said. “Corn ethanol, for example, requires acres of cropland, as well as fertilizers, pesticides, irrigation and fermentation. Methanogens are much more efficient, because they metabolize methane in just a few quick steps.”
Microbial communities
For this new technology to become commercially viable, a number of fundamental challenges must be addressed.
“While conceptually simple, there are significant hurdles to overcome before electricity-to-methane technology can be deployed at a large scale,” said Bruce Logan, a professor of civil and environmental engineering at Penn State. “That’s because the underlying science of how these organisms convert electrons into chemical energy is poorly understood.”
In 2009, Logan’s lab was the first to demonstrate that a methanogen strain known as Methanobacterium palustre could convert an electrical current directly into methane. For the experiment, Logan and his Penn State colleagues built a reverse battery with positive and negative electrodes placed in a beaker of nutrient-enriched water.
The researchers spread a biofilm mixture of M. palustre and other microbial species onto the cathode. When an electrical current was applied, the M. palustre began churning out methane gas.
“The microbes were about 80 percent efficient in converting electricity to methane,” Logan said.
The rate of methane production remained high as long as the mixed microbial community was intact. But when a previously isolated strain of pure M. palustre was placed on the cathode alone, the rate plummeted, suggesting that methanogens separated from other microbial species are less efficient than those living in a natural community.
“Microbial communities are complex,” Spormann added. “For example, oxygen-consuming bacteria can help stabilize the community by preventing the build-up of oxygen gas, which methanogens cannot tolerate. Other microbes compete with methanogens for electrons. We want to identify the composition of different communities and see how they evolve together over time.”
Microbial zoo
To accomplish that goal, Spormann has been feeding electricity to laboratory cultures consisting of mixed strains of archaea and bacteria. This microbial zoo includes bacterial species that compete with methanogens for carbon dioxide, which the bacteria use to make acetate – an important ingredient in vinegar, textiles and a variety of industrial chemicals.
“There might be organisms that are perfect for making acetate or methane but haven’t been identified yet,” Spormann said. “We need to tap into the unknown, novel organisms that are out there.”
At Penn State, Logan’s lab is designing and testing advanced cathode technologies that will encourage the growth of methanogens and maximize methane production. The Penn State team is also studying new materials for electrodes, including a carbon-mesh fabric that could eliminate the need for platinum and other precious metal catalysts.
“Many of these materials have only been studied in bacterial systems but not in communities with methanogens or other archaea,” Logan said. “Our ultimate goal is to create a cost-effective system that reliably and robustly produces methane from clean electrical energy. It’s high-risk, high-reward research, but new approaches are needed for energy storage and for making useful organic molecules without fossil fuels.”
The Stanford-Penn State research effort is funded by a three-year grant from the Global Climate and Energy Project at Stanford.
Source: Mark Shwartz, Stanford University News
Image: L.A. Cicero